Europe News
This sustainable, 3D-printed house in Portugal is a thing of beauty
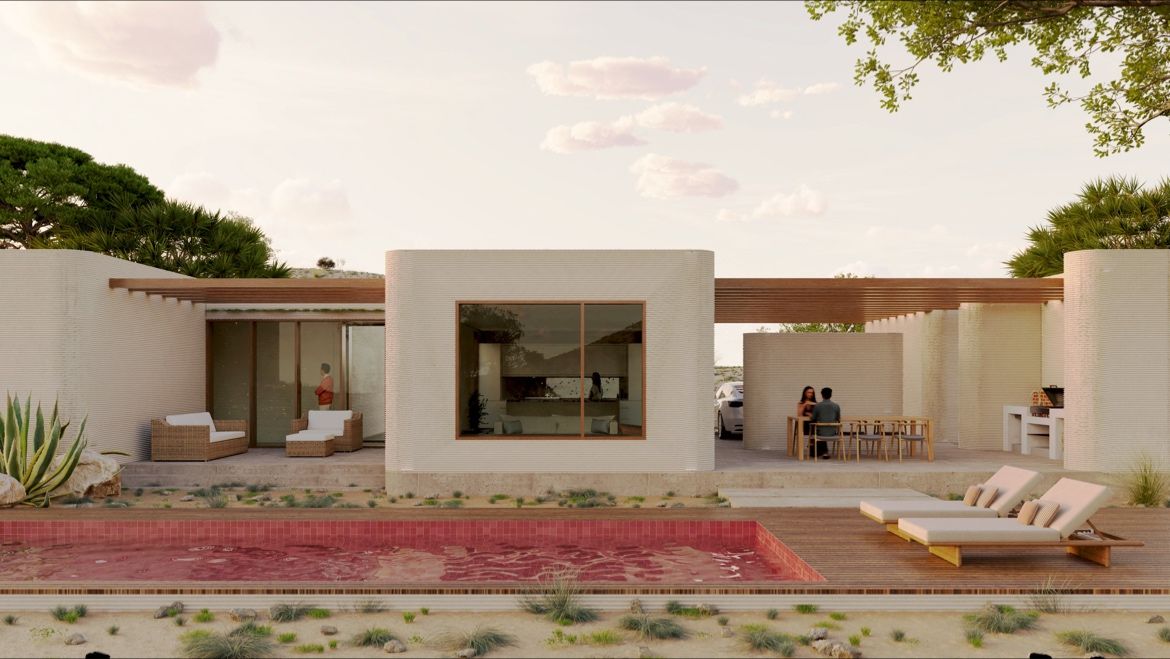
Litehaus announced the winner of its competition to find the first Portuguese architect to build a 3D printed house in the country
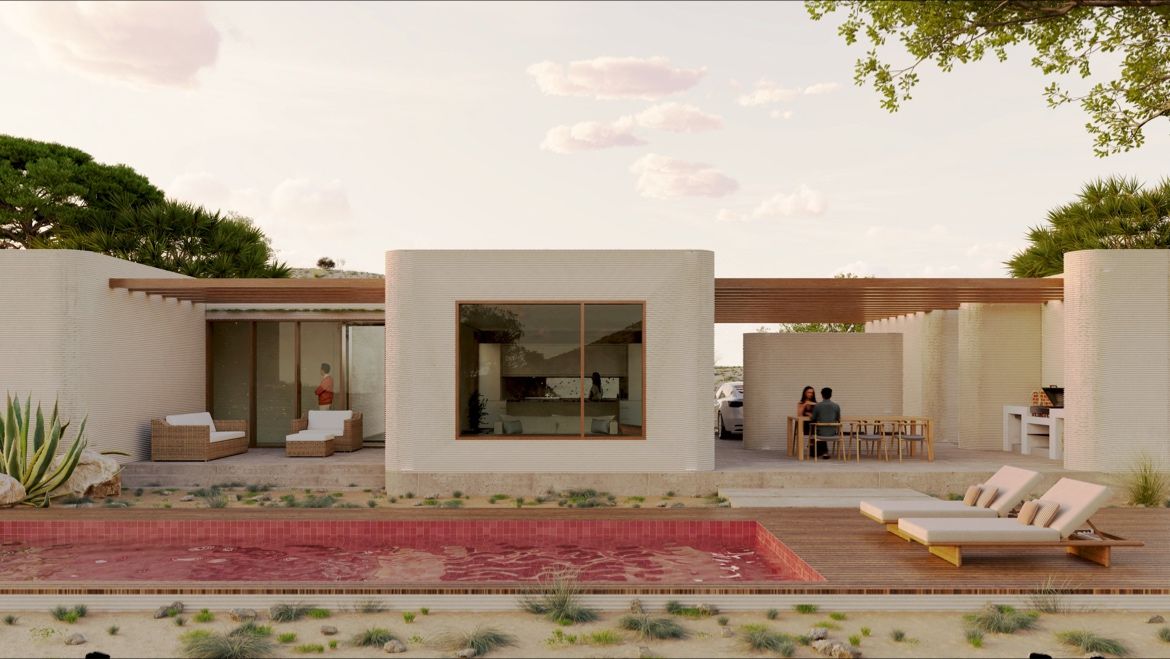
Litehaus announced the winner of its competition to find the first Portuguese architect to build a 3D printed house in the country
Property development company, Litehaus, has awarded Braga architect Rui Barbosa €5,000 to design the first 3D printed house in Portugal. The 300 square metre house is inspired by the nearby beach air and street ambiance of nearby Comporta and Melides. Modular in character, the house’s design features a pool with red tiles and brownish and beige tones. Rooms connected by a central corridor can be organised according to the inhabinant’s wishes within the terrain confines.
“In the proposal with which I competed, I tried to combine this new construction method with modular repetition,” said Rui Barbosa. “I tried to combine contemporary elements with the traditional architectural language of Melides, always respecting the urban context.” This new villa will be part of the zero waste housing network built using Litehaus’ Artificial Intelligence, 3D printing and modular technology, which is expanding throughout Portugal.
According to Litehaus, the 3D-printed construction market is expected to grow 88 per cent each year, potentially achieving a worth of about 400 billion dollars by 2030. “We want to be part of this evolution, contributing to a milestone in the history of Portuguese architecture,” stated Simi Launay, Litehaus’ Chief Creative Officer. “With the goal of building 100 houses per year in Portugal, we’re going to complement the 13-house residential unit in Torres Vedras with this new building in Melides, with Rui’s invaluable help. At the same time, we have another 50 projects planned for Torres Vedras, 73 modular tourist flats in Braga and we’re currently close to finalising a 108-room development for students in Famalicão.”
Cosmos, a Spanish company with 3D printing technology, will partner with Litehaus on the project. 3D printed homes, according to Litehaus, can consume up to 70 per cent less energy to manufacture while reducing construction time. The home’s walls are made of ECOMortar, producing between 40 and 50 per cent less CO2 emissions. Litehaus aims to be building in five years’ time at a price 50 per cent lower than traditional manufacturing.
Latest Articles
Don't miss the latest from Luxury Travel